6 mins read
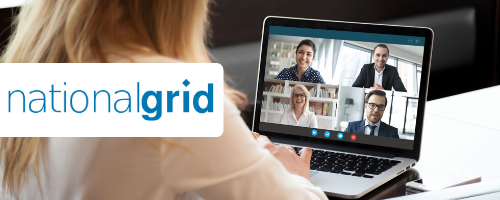
Matthew Goldberg discusses UKAS’ flexible approach and how remote assessments have benefited their business.
Related topics
The onset of the Covid-19 pandemic meant organisations had to quickly adapt their ‘normal’ working practices to fit in with government guidelines on social distancing. Recognising that many accredited organisations needed to maintain their accreditation for legal, practical or business reasons during the lockdown, UKAS quickly brought forward its plan to introduce remote accreditation assessments.
One of the first companies to experience remote accreditation assessments was National Grid Gas (NGG). Part of National Grid plc, NGG owns, manages and operates the national gas transmission system (NTS) in Great Britain which stretches from St Fergus Terminal in Scotland, to Bacton in England and Milford Haven in Wales. Each day NGG could utilise over 60 gas turbine driven mechanical drive compressors located at 23 gas compressor stations and 2 gas terminals to transport between 200-400 million cubic meters of gas through 7200km of pipeline, where it is used for everything from heating and cooking in homes to power generation and fueling industrial processes.
Relying on accreditation
NGG’s compressor stations are classed as Part A permitted installations by the Environment Agency, Scottish Environment Protection Agency and Natural Resources Wales and as such are required to undertake emission monitoring for compliance purposes using ISO 17025 accredited stack emission monitoring laboratories. In England and Wales personnel and organisation MCERTS accreditation is also required. MCERTS provides a quality framework for measuring stack emissions and Environment Agency policy requires all laboratories submitting results for regulatory purposes to be accredited to the MCERTS standard. Rather than use an external laboratory to gather these results, NGG chose to establish its own laboratory as a key part of its emissions monitoring team. Matthew Goldberg, NGG’s Environmental Assurance Manager commented:
“We carry out stack emissions monitoring at all our Part A installations and perform over 50 accredited stack emissions tests per year. The unique demands of our industry and varying grid conditions means that we need the flexibility to be able to change test dates on a weekly basis, this is only really possible with an internal testing laboratory.”
NGG’s laboratory has been accredited by UKAS for 20 years and was due its annual assessment visit at the beginning of April. The sudden imposition of the UK’s lockdown measures meant that both UKAS and NGG had to act quickly to maintain NGG’s accreditation so that it could continue to meet Environment Agency requirements. Matthew said:
Maintaining our laboratory’s UKAS ISO 17025 accreditation is vital in order to meet permit requirements. It’s one of the most fundamental parts of our critical path, as without accreditation our laboratory test results are invalid, meaning we couldn’t demonstrate compliance with the regulations and would not be permitted to move gas around the country.
Adapting processes
In light of the potential threats to health and safety posed by Covid-19, both UKAS and NGG implemented remote working practices. This fundamentally altered the format of the accreditation assessment as Matthew Williams, Environmental Assurance Engineer and Quality Manager explains:
Normally we would set aside a couple of days for the UKAS assessment team to visit our offices to go through the relevant documentation and processes, and a further day for witnessing of testing activities at one of our sites. With all our sites closed to non-critical staff and UKAS only conducting remote assessments, we had to be flexible about how to manage our accreditation assessment.
Rather than evidence the quality management documentation on the day and in person, our assessment manager provided a list of documents and evidence they wanted to see, which we collated and e-mailed in advance of the due assessment day. Although circumstances meant we had to be agile to gather everything together remotely, providing the evidence in advance was no greater pull on overall resources or time than if we had done it face to face on the day. Security was also a potential issue for NGG, but any concerns were quickly allayed by UKAS. Matthew said:
As a major part of the UK’s national infrastructure, information and cyber security are very high up our agenda. We’re very limited in what IT systems we can use, but UKAS was flexible enough to utilise our approved conferencing and document sharing systems. It also provided the requisite assurance that any information we sent would be kept in the strictest confidence and only shared with the authorities as necessary.
NGG and UKAS established a timetable to go through the evidence and agreed a schedule of Q&A sessions. This more fragmented and flexible assessment process worked well for NGG, Samuel Brookes, Environmental Assurance Officer and Technical Manager explains:
Spreading out the assessment over a longer timeframe means we can carry on with our day jobs whilst UKAS reviews the evidence. Any issues can be addressed via regular touch points or a quick phone call, and any requested documents e-mailed immediately afterwards. Although the assessment takes longer from start date to finish date, the total time spent on the process is the same.
Witnessing from afar
The witnessing of activity is a major part of an assessment visit and those participating in remote assessment are being encouraged to provide live webcams or narrated video recordings of activities to satisfy that element. However, UKAS recognises that this may not be possible, so has discretion to postpone the witnessing element in certain cases whilst maintaining accreditation. NGG is one such case, as Matthew Williams explains:
The nature of the testing process and potentially hazardous environment is such that our testing cannot be witnessed remotely via a webcam or recording. It must be witnessed in person, which is not possible given the current movement restrictions. As NGG has been accredited for a number of years, we’ve successfully passed several site witnessed tests before. UKAS has taken this track record into consideration when assessing our risk of non-compliance, and has agreed to maintain our accreditation and reschedule the witnessed testing element to when restrictions on movement are lifted.
Summary
Reflecting on the overall experience of remote assessment, Matthew Goldberg concluded:
It was great to see that UKAS is open to new ways of working and UKAS’s flexible approach meant remote assessments really benefitted us an organisation. Despite our initial impression, planning ahead and compiling the documentation in advance involves no additional work as you’re effectively just changing the timing around. If anything it’s a streamlined and more efficient method, as remote assessment has a lower overall impact on resources, with the added benefit of being able to fit it in around other work demands. From our experience we would warmly welcome the option of remote assessment when things get back to ‘normal’ and would certainly recommend it for other organisations due a maintenance accreditation visit.