3 mins read
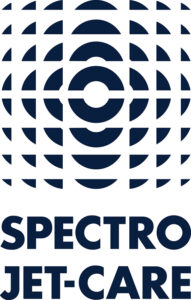
Related topics
Jet-Care International provides a comprehensive range of laboratory analysis services to the aviation, marine and industrial market sectors. Their services include analysis of oil, hydraulic fluid, fuel, grease, coolant, transformer oil, fuel, debris and filters, leading to the identification of potential problems with engines, gearboxes, critical control systems, generators and fuel tanks. The results of the analysis they provide, and the data gathered, can identify operational issues at the earliest possible stage helping their customers to avoid possible failures, improve productivity and meet safety requirements. Last year, Jet-Care celebrated their 20th year of being a UKAS accredited testing laboratory and are currently accredited against the latest version of the standard, ISO/IEC 17025:2017.
In this short interview below, Alison Potere, Continuous Improvement Manager at Jet-Care, speaks about their experience of their recent UKAS remote assessment.
How did you prepare for your remote assessment?
The preparation was initiated by our Assessment Manager several weeks prior to the assessment. Our Assessment Manager was well prepared and gave us concise instruction as to what would be needed. Along with the remote assessment agenda, a request was made for us to submit documentation encompassing the items due for review prior to the assessment. These were easily retrieved as most of our documents and files are kept electronically.
What technology was used during the assessment?
We used Microsoft Teams for the opening and closing meetings, as well as an interim progress meeting to touch base and discuss any issues or difficulties we may have been having. Our Assessment Manager, Sarah, was very patient with us as we learned to connect with Teams. We found it to be an effective way to communicate. In fact, it improved our communications as questions could be asked, explanations made, and related topics discussed. Our documents were easily sent via email as and when requested throughout the assessment.
Was the approach to the assessment of technical activities any different?
The assessment activity was configured in a way that evidence could be gathered from a specific point in time given by the assessors to confirm the effectiveness of the methods selected. Samples were traced from beginning to end using the same data that would have been reviewed with an onsite audit. Interaction between the assessor and the laboratory was by email and was found to be effective.
How did you find the format of a remote assessment?
We found the remote audit to be efficient and less disruptive to employees’ regular workflow, as well as cost effective since flights or hotel accommodations were not needed.
Did you encounter any difficulties/challenges during the assessment?
We did not experience any difficulties. The whole process went very smoothly. Everyone was well prepared.
Any advice for other companies facing a remote assessment?
Have as much of your documentation held electronically as possible and ensure your electronic filing systems are organized so that you can retrieve data and documents effortlessly throughout the assessment.
Would you do it again?
Yes.